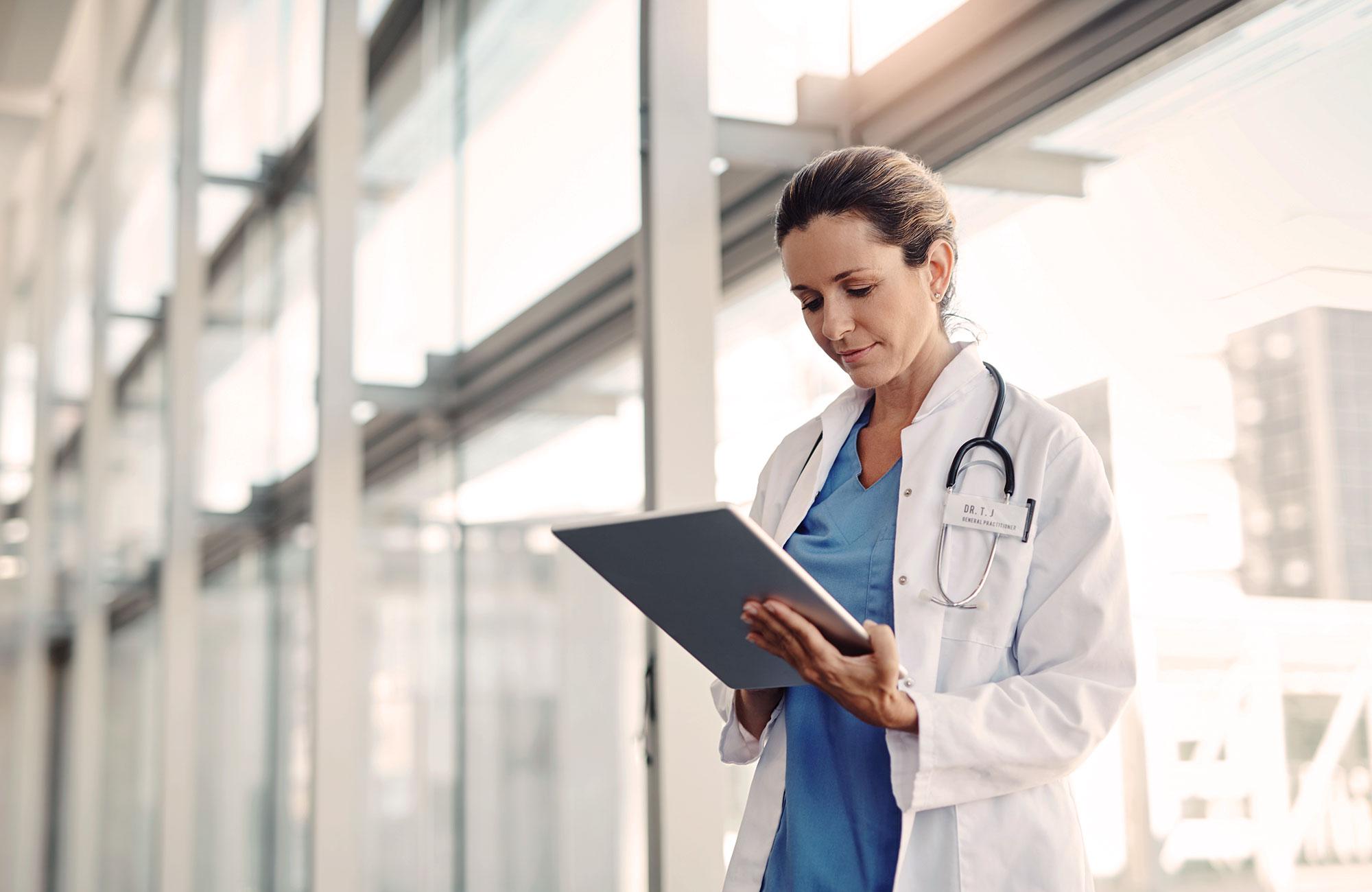
In terms of digitalization, there has been a lot of progress in the life science industry since spring 2020, which would most likely have taken years had it not been for a global pandemic: The closing of many facilities and social distancing regulations have resulted in accelerated implementation and a desire for digital solutions, such as telehealth concepts or remote patient monitoring, to name a few. A survey by Deloitte on the state of digitalization in the European healthcare system, however, shows that there is still room for improvement:
About 65 percent of staff surveyed said their respective organizations have increased the use of digital technologies to support the way they work and to facilitate patient access.
Among physicians, about three-quarters said their organization has increased its use of digital technologies.
Technology adoption to change the way people work, however, varies widely within Europe's healthcare industry. While 83.6 percent of Norwegians are already in favor of digital solutions, this figure is currently only 39.6 percent in Germany.
The four requirements of the MDR: Reasons for digitalization
MDR is a way to help everyone who notices their digital progress has been stalling. The new regulation is intended to help ensure that the quality of all medical devices used in the EU is up to par with the best, while establishing equal rules for all. This entails changes in terms of traceability of quality, performance and safety of medical devices. However, it also strives to make analog processes a thing of the past as far as possible, given that they are too susceptible to errors. Four changes to the MDR are driving digitalization:
The scope extension significantly expands the definition of medical devices and active implantable medical devices covered by the MDR. In the future, more products will have to be covered and more companies not previously affected will be covered by the MDR.
The MDR prescribes the use of UDI (Unique Device Identification) mechanisms to implement unique product identification. This is designed to increase the ability of manufacturers and regulators to track specific products through the supply chain and facilitate the quick and efficient recall of medical devices that have been identified as posing a safety risk. The effort required to draw regulatory conclusions will therefore increase.
The MDR requires strict post-market clinical surveillance by the designated authority. Unannounced audits, product sample inspections and product tests will be carried out to reduce risks from unsafe products. In many cases, annual safety and performance reports from product manufacturers will also be required.
There will be no "grandfathering”: all medical devices currently marked as CE will have to be CE-certified again according to the new requirements. Exceptions are still being negotiated. As of now, nonetheless, all products will need to be reprocessed.
Challenge vs. opportunity – consequences of the MDR
More products to consider, stricter documentation requirements, detailed traceability and the requirement to recertify every product already registered. In light of the new requirements, analog processes or solutions in Excel represent a real hurdle – at the very latest when an unannounced audit takes place. It is no longer sufficient to manage processes and documentation around approval and quality assurance on paper. Even completely separated data stores lead to data silos that are difficult to monitor. And existing solutions, such as parts lists in SAP, client and supplier information in CRMs, and product information systems (PIMS), are only just beginning to meet the requirements.
The solution: Automation and digitalization
To achieve the best possible synergies and build on existing solutions, however, creating a centralized system seems appropriate. Existing solutions and data can be integrated into such an open system. All necessary information from different departments and stakeholders can be accessed in one place. Companies can use it to manage suppliers, create and coordinate tasks, insert marketing and product data, and provide access to information individually for different stakeholders so that they can use services and information that are relevant to them. This involves managing and orchestrating the relevant processes on a single platform, rather than creating yet another data repository. By automating and digitalizing business processes, hurdles with regard to the MDR are eliminated and, at the same time, companies save costs in the medium and long term while minimizing risks of damage to their image.
With agile project design to products with added value
Anyone who thinks that implementing a digital solution is a huge project of unimaginable proportions is mistaken. Ultimately, it is about analyzing the customer's needs precisely and setting up a customized solution. The requirements imposed by the MDR and the time frame allow for an iterative approach. For example, a sub-project or a specific product group can be started before the solution is rolled out to the entire portfolio. At Mimacom, we work in accordance with an agile project design and develop products according to the human-centered design approach. In other words: The company focuses on the user and their needs and develops a suitable product step by step, based on user stories and feedback. The result: Planning and investment security throughout the entire project.
Mimacom's Digital Accelerator Program follows a development approach that addresses current and future requirements.
At the heart of the Digital Accelerator Program approach is understanding and planning the project (Learning). The goal in each case is to refine precisely those aspects that are relevant to the overall solution. To take the first step towards a viable solution, technical and content-related customer needs must first be understood (Understand). For this purpose, Mimacom systematically records the requirements. Ideas for the optimal solution can emerge on this basis (Ideate). Throughout the process, we will be working together with the customer, and in the next phase we will therefore jointly develop the first prototype, based on the knowledge gained so far. Tests will show at an early stage whether a product will deliver the required results. This will provide the software expert with market feedback and acceptance criteria. Once user and business requirements are aligned and the core designs are created, the iterative implementation (Develop) can begin.
Thanks to this approach, an initial product (MVP) is very quickly created and then optimized by further iterations. In this way, an initial product can be created in just a few weeks and with a small investment, which is continuously improved depending on feedback and budgeting. The user acceptance ultimately dictates whether the products are successful after the first loop or whether there is a need for optimization. In any case, according to the company, the end result is a product with the highest usability and excellent user experience.
Tim Weinmann
Based in the US, Tim is our CRO for the global Mimacom company. He is a passionate leader with a focus on Sales and Marketing.