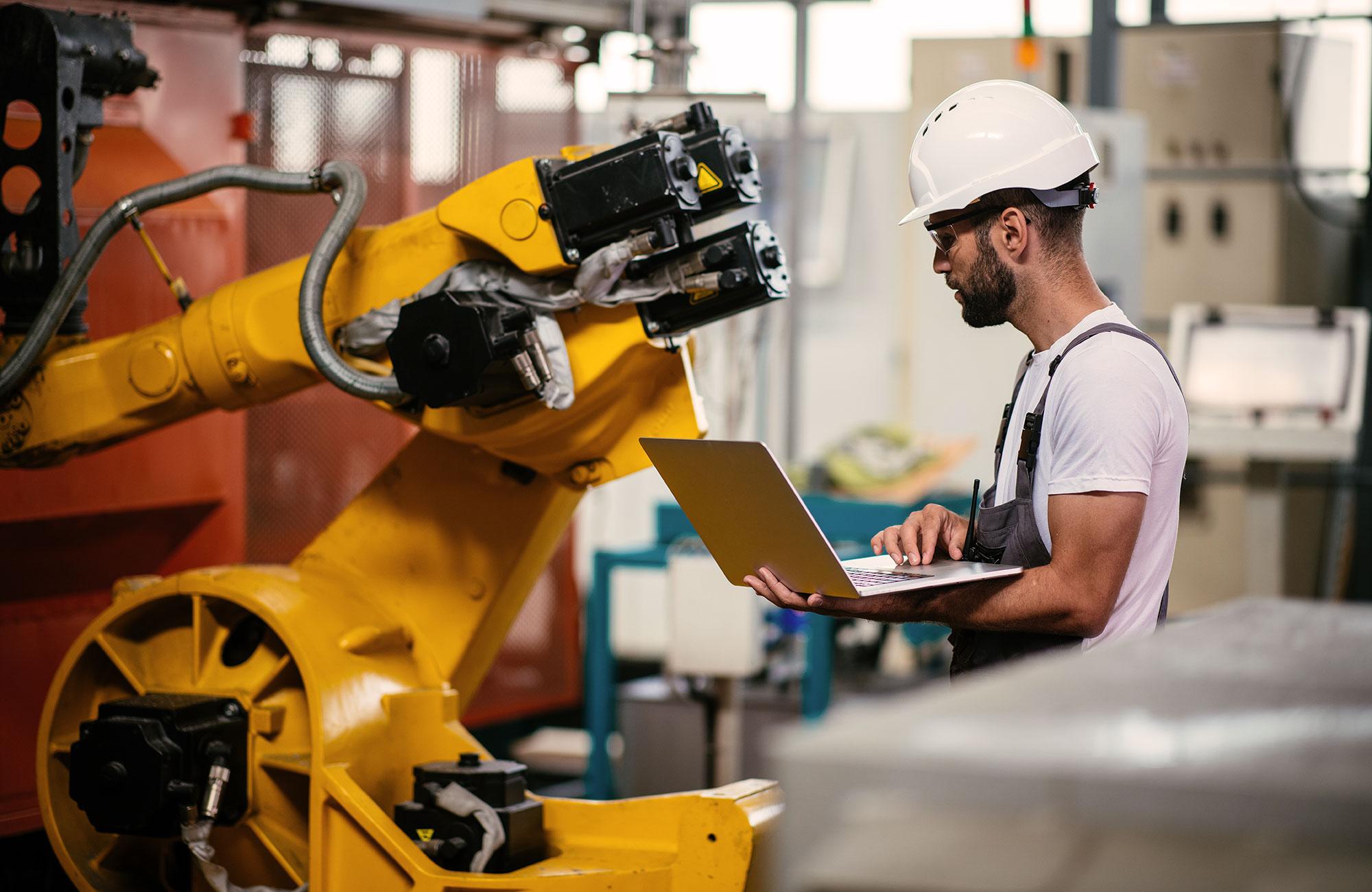
The classic products and services that have made machinery and plant manufacturers successful today are no longer enough. Machinery and plant manufacturers strive to continuously boost the efficiency of their customers with services that are tailored to their needs. This requires technologically well positioned companies that can give their customers flexible and swift support. Offering online services via IoT cloud platforms is thus a crucial success criterion in the ongoing digital transformation.
The challenge: Developing customer-centric services
The demands on companies in a data-driven business environment have changed drastically in recent years. Machine and plant manufacturers face the challenge of constantly having to adapt to the rising expectations of their customers and changing market needs. They also need to analyze and manage ever larger volumes of increasingly complex data. A cloud-based approach to work can help companies and allow faster and easier adaptation when expanding their service portfolio.
Only companies that are aware of their customers’ needs, after all, can offer appropriate services. From the customer’s point of view, what matters is identifying use cases that create real added value. Data analysis via real-time data streaming through IoT customer portals plays a crucial role here, providing insights into user behavior and trends on the customer side.
Analyzing this information not only allows machine and plant manufacturers to improve their existing services, prepare suitable product information and offer after-sales support, but also helps them draw conclusions about customer demand, process efficiency, service availability and much more. Companies that recognize trends can meet these customer and market requirements with the appropriate services. Cloud computing therefore focuses on improving not only process efficiency but also performance management in order to provide the best possible customer services.
The solution: Digital value creation through cloud engineering
Digitalization is changing the machinery and plant manufacturing sector faster than ever before. Providers from outside the industry are increasing the competitive pressure. New, data-driven services via clouds and portals are for this reason also important when it comes to boosting value creation. Many IoT projects in the service sector in particular can already be implemented quickly and for plannable costs. This results in a fast ROI, as digital services pay off for customers in the short term. They are also easily scalable, which in turn makes them very profitable.
Leveraging cloud service to boost business success
A precise digital strategy tailored to the respective plant and machine manufacturer is the cornerstone for providing digital customer services. IoT cloud platforms are an important component of any such strategy, as they allow the digital monitoring of relevant customer, machine and process data while uncovering inefficiencies. The collected data forms the basis for a wide range of online services that provide plant and machine manufacturers and their end customers with an excellent user and customer experience.
Fast time-to-market: Linking existing systems via an IoT cloud platform enables optimal interface networking. This results in faster data exchange and consistent data, so reducing time-to-market.
Optimize performance and availability: Cloud platforms are available 24/7 to both customers and employees.
Simplify big data management: IoT platforms benefit data-centric companies by making it easy to manage and analyze large and complex data sets.
Optimize the user journey: Real-time data streaming via cloud portals gives companies up-to-date information on machines, maintenance, obsolescence man-agement, performance and individual requests.
Conclusion: Data-driven services enable successful customer relationships
The potential of new data-driven services for machine and plant manufacturers is based on long-term customer relationships. They provide both plant manufacturers and their customers with a wide range of added-value options. For example, companies can generate revenue from maintenance and cloud-based services over a machine’s entire life cycle. Complaint costs can also be reduced by optimizing machines through monitoring, so preventing any malfunctions on the customer’s premises. The benefits for customers include higher productivity through better machine utilization as well as reduced downtime and maintenance costs.
Fabian Kleiser
Located in Stuttgart, Germany, Fabian is our Head of Cloud Innovations in Germany. As a Software Engineer, he leads strategic Cloud Foundry implementations at Mimacom and is known for his passion for code quality, automation and simplicity.